CS/ONH-ANALYSIS (CS/ONH)
G6 LEONARDO
Economic Quality & Process Control for O/N/H.
Simplicity @ its best
SampleCare™ & FusionControl ensure reliable results
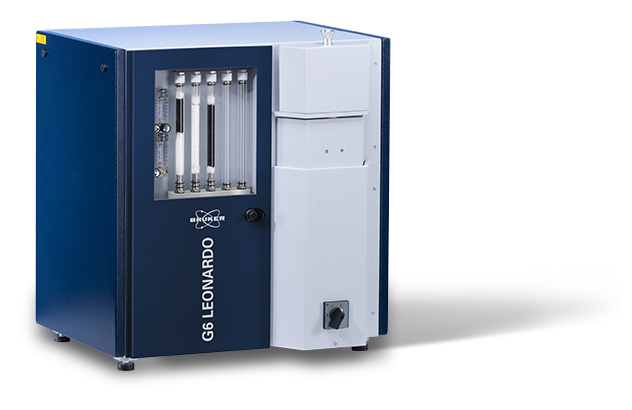
High-precision, easy-to-use and robust Inert Gas Fusion analyzer
ppb (ng/g)
Limit of Detection for Hydrogen and Nitrogen
The high-end thermal conductivity detector used for hydrogen and nitrogen analysis allows detection limits in a sub-ppm range (based on 1g sample mass)0 l/min
Consumption of compressed air
The lower electrode movement by EZDrive eliminates the need for additonal working gases, ensures an ideal contact between crucible and electrodes to provides enhanced safety and reliability.> 3000 °C
Achievable by the advanced electrode furnace for refractory samples
The water cooled electrode furnace is equipped with FusionControl for precise temperature control. SampleCare™ includes an integrated maintenance-free sample port shielding the sample from undesirable heat.G6 LEONARDO – Economic Quality and Process Control by Inert Gas Fusion
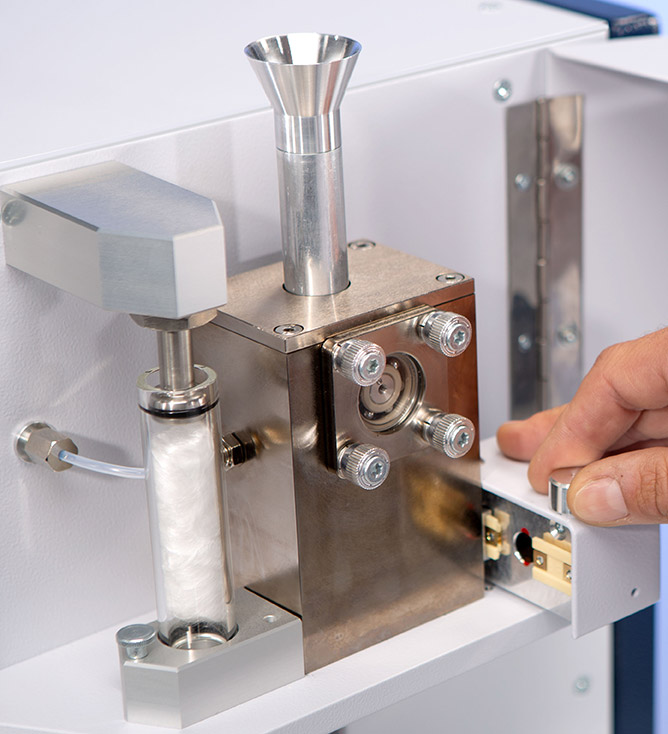
Electrode Furnace with SampleCare and FusionControl
Electrode Furnace with SampleCare and FusionControl
The three non-metals Oxygen (O), Nitrogen (N) and Hydrogen (H) determine the quality, service life and mechanical properties of all metallic materials. Unlike metallic alloy components, the amount of O, N and H sometimes changes considerably along the entire process chain, from the production of raw materials to the completion of the finished product. Even when present in trace amounts, O, N and H have a very critical effect on the material properties.
The G6 LEONARDO is based on the inert gas fusion (IGF), which involves fusion of the sample material in a graphite crucible at high temperatures. This principle is also commonly termed gas fusion analysis (GFA) or melt extraction (ME) since the total oxygen, nitrogen and hydrogen is extracted by an inert carrier gas when the sample melts.
The Smart Molecule Sequence™ guarantees trustworthy results
The aim of an IGF analysis is to determine the sample content of the light elements O, N and H in the trace range with absolute accuracy. That is why our G6 LEONARDO applies the Smart Molecule Sequence™ and measures the gases emitted by the sample directly, absolutely unchanged, 1:1, with proven scientific principles for trustworthy results. It also allows oxygen determination without additional chemicals, and usage of argon carrier gas instead of helium ensuring high reliability and low cost of ownership.
Key Benefits
- FusionControl™: Ongoing contact free temperature measurement of the sample
- SampleCare™ for IGF analysis consisting of EZDrive, water cooled sample port, high capacity dust trap, followed by efficient in-line particle filtering
- Smart Molecule Sequence™: Direct and unadulterated measurements of all emitted gases by state of the art detectors with reference channels.
- FUSION.ELEMENTS™: Future-save easy to use software based on Bruker’s Alaska platform
Optimized with user-friendly features
SampleCareTM, Smart Molecule SequenceTM including FusionControl and ready-to-use precalibrated methods for many industrial standard applications make the G6 LEONARDO a great choice for process and quality control in primary metal manufacturing and processing, ceramics, and powder metallurgical processes.
G6 LEONARDO Applications
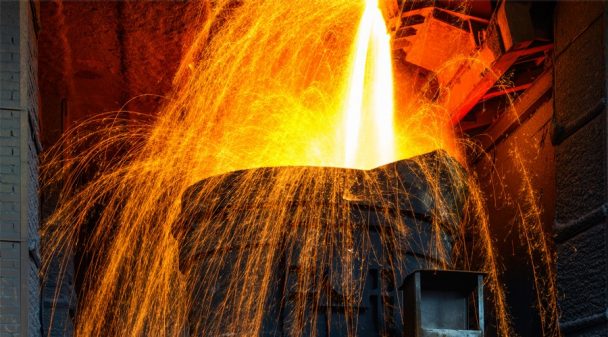
Iron, Steel, Cobalt, Nickel, Ferroalloys
Determining the amount of oxygen and nitrogen is critical during the steel making process, the final alloy adjustment by addition of ferroalloys but also for the production of nickel- and cobalt-base alloys. The G6 LEONARDO combines the ease-of-use and robustness to deliver fast and accurate oxygen and nitrogen results for the Quality- and Process-Control in these production processes.
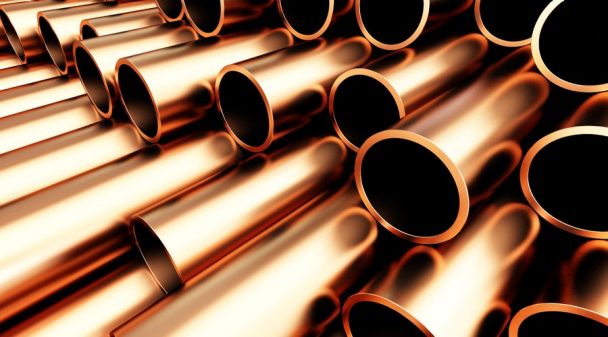
Copper Production
The most important quality factor when grading copper is the level of residual impurities, primarily the oxygen level. High oxygen levels increase the tendency for hydrogen embrittlement and intergranular failure. The Smart Molecule SequenceTM, ensures the G6 LEONARDO analyses oxygen with high reliability and low cost of ownership, while precise simultaneous oxygen and hydrogen analysis is available in dual element configurations with FusionControl.
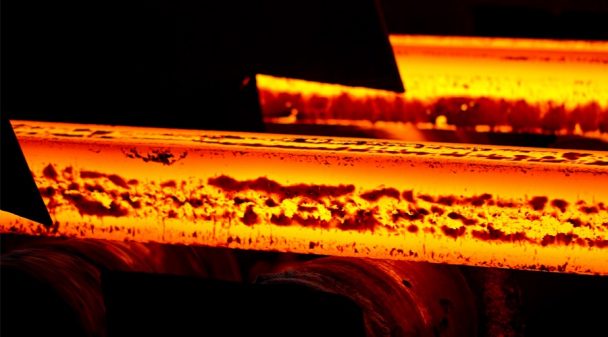
Titanium, Zirconium and other Refractory Metals
Titanium combined with elements like aluminum, vanadium, molybdenum produces low-density, high-strengths alloys with excellent corrosion-resistance. These high performance alloys used in space, aviation, military, nuclear, biomedical and other demanding applications are affected by their oxygen and nitrogen content, but the most critical specification is the hydrogen content leading to hydride precipitation and subsequent cracking. The G6 LEONARDO is prepared to address the needs of these demanding industries.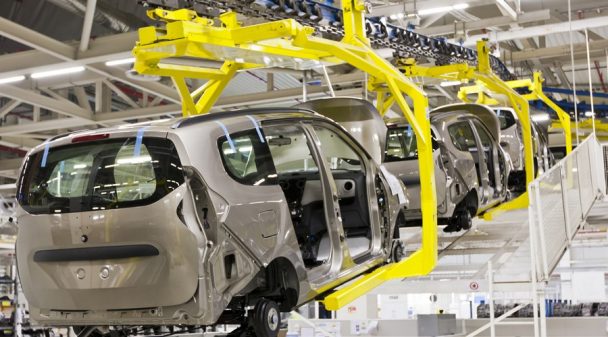
Metal Processing
From stainless steel, aluminum, copper, nickel, titanium to zirconium and further special metal compositions, the G6 LEONARDO delivers vital knowledge about the chemical material composition to every demanding metal processing task in aviation, space, automotive, biomedical, electronic and similar industries.
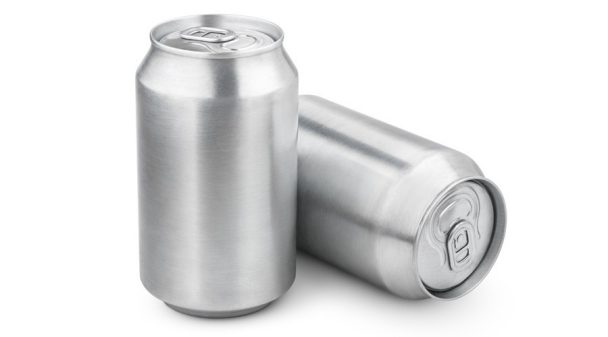
Aluminum and Magnesium
Oxygen and hydrogen play a dominant role during the production and processing of these reactive light metals. Oxygen forms insoluble, refractory inclusions whereas hydrogen, dissolved in the liquid melt, is trapped during solidification, creating hydrogen filled voids and blisters. With its unique FusionControl and SampleCareTM, the G6 LEONARDO is an ideal quality control tool for the aluminum producing industry.
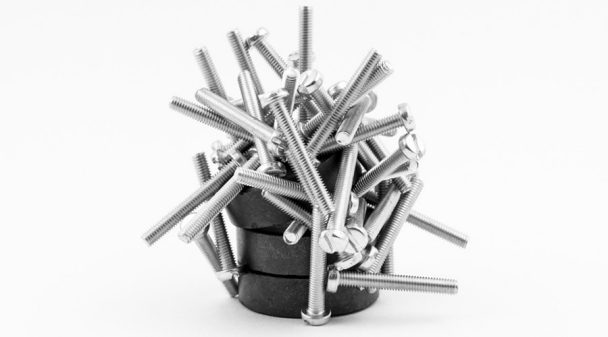
Magnetic Materials
The evolution of high strengths permanent magnets is related to the application of rare earth metals. Sintered Nd-Fe-B magnets show a high tendency to absorb hydrogen, leading to fatal hydrogen embrittlement. Actually, hydrogen is a vital agent in the manufacturing process but is also during recycling of the rare earth metal, while oxygen reduces the magnetic efficiency. The G6 LEONARDO is an economic and easy-to-use tool for process control on both elements during all production stages.
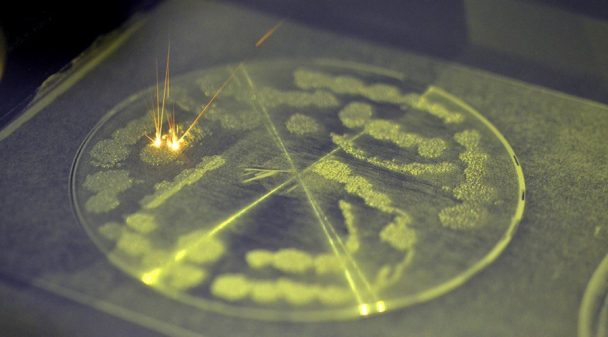
Powder Metallurgy and Additive Manufacturing
Metal powders used in additive manufacturing and other powder metallurgical processes are high purity materials with strictly defined particle properties. Their large specific surface makes them susceptible to “aging” by oxidation/moisture along the production chain with oxygen and hydrogen content dominating the yield rate and product quality. The ready-to-use G6 LEONARDO addresses the needs of such emerging industrial applications.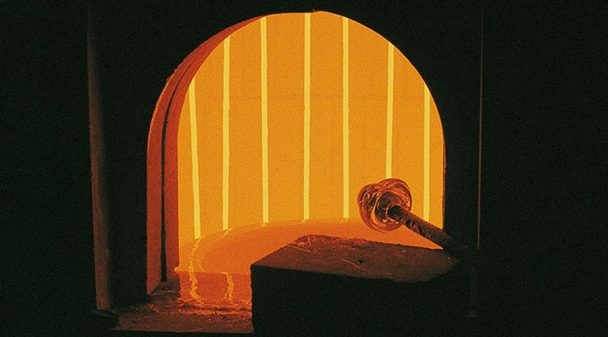
Glass & Ceramics
From industry refractory materials to high performance ceramics in electronics or in metal cutting, refractory oxides, nitrides and carbides have a wide usage. The unique properties of glass and ceramics are influenced in fundamental ways by the level of oxygen, nitrogen and hydrogen present in the process or in the final product. With SampleCareTM, FusionControl and its robustness, the G6 LEONARDO is an excellent tool for the fast analysis of raw materials, intermediates and final products.G6 LEONARDO Specifications
Specification | Benefit | |
---|---|---|
Sample | ||
Sample Types | Inorganic, dry, any form or shape | Flexibility |
Sample Dimensions | 8 x 8 mm cross section (pieces, chips, pins, granules), different sample ports available for special applications | Wide variety of sample materials |
Detectors | ||
Oxygen | Nondispersive IR absorption of CO, no moving parts, multiple range detectors with reference beam and on-board linearization | Reliable, maintenace-free performance without drift |
Nitrogen and Hydrogen | Thermal conductivity detector with reference channel and adjustable gain amplifier | Reliable, adjustable ranges, drift free |
Furnace | Water-cooled Electrode Furnace with FusionControl | Solid high temperature operation for refractories, precise temperature control |
SampleCare™ | ||
EZDrive | Lower electrode movement by reliable electronic motion module | Robust, cost-saving operation without working gas. Automatic, torque limited readjustment ensures ideal crucible:electrode contact and safety for crucible, furnace and operator. |
Sample Port | Rotating sample port integrated into water cooled furnace block | Shields sensitive samples from heat input and hydrogen losses before analysis. Allows capsule-free measurement of grains without jamming. |
Particle Filtering | High-capacity dust trap followed by in-line particle filtering | Stable analytical results with reduced maintenance and component protection |
Cooling Water | 4 l/min at 3 bar supply pressure | Fits on every usual tap water line, tap, water-saving design with solenoid valve, chiller also possible |
Carrier Gas | Ar (O, N), He (O, N), N2 (H) each 99.995 % purity (99.9990 % for trace analysis) | Flexible carrier gas choice without compromises |
Noise Emission | < 55 dB(A) peak | Enjoy the silence |
Calibration | Single and multipoint calibration, advanced weighting algorithm with error bars and range merging | Easy simultaneous calibration of all ranges with confidence |
Reagents |
| |
Power Supply | 400 – 480 VAC (± 10 %), 50-60 Hz, 32 A, 7 kVA, 1 Phase plus N or 2 Phase, grounding wire 230 VAC (± 10 %), 50-60 Hz, 64 A, 7 kVA available as option | Compatible to worldwide power and current configurations |
Models Available | Single or dual element O, N, H, ON, OH | Ideal tool for process and quality control |
Dimensions and Weight | 71 x 66 x 78 cm (W x D x H), ~145 kg | Compact form, easy to maintain |
*) Depending on configuration |