CS/ONH-ANALYSIS (CS/ONH)
G8 GALILEO
High-end analyzer, designed for automatic and precise determination of O/N/H
The most versatile system available
Mass spectrometric detection capabilities
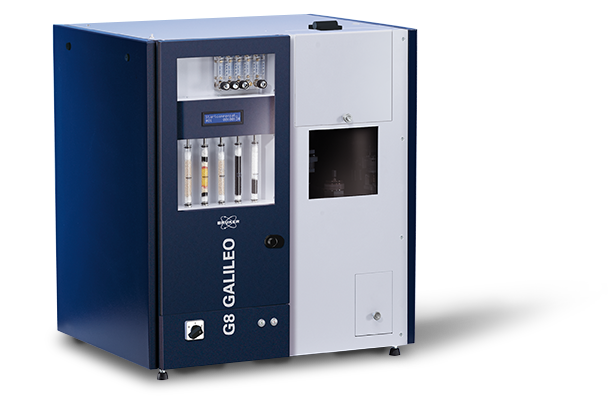
High-end designed for accuracy @ high-throughput
ppb (ng/g)
Limit of Detection
All state-of-the-art detectors used in the G8 GALILEO are equipped with internal reference channels for utmost stability and allow detection limits in a sub-ppm range (based on 1g sample mass)0-100 amu
m/z range of mass spectrometer (MS)
The industrial-grade MS is tailor made for hydrogen and argon detection, equipped with an optimized ion source and channeltron detector. With an extremely efficient gas inlet system, it delivers detection limits in the lower ng/g range, equivalent to a particle density of a few molecules.3+ analyzers
In one single system
Whether the task is O/N/H analysis with real H2-detection by TCD, reliable sub-ppm determination of H in high purity Al, diffusible & residual Hydrogen in welds, or argon inclusion analysis of powder feedstock for additive manufacturing, or in final parts: the G8 GALILEO can be equipped to fulfill almost every analytical challange.
Matching the best ONH method – Inert Gas Fusion – with the ideal ONH systems: G8 GALILEO and G8 GALILEO MS
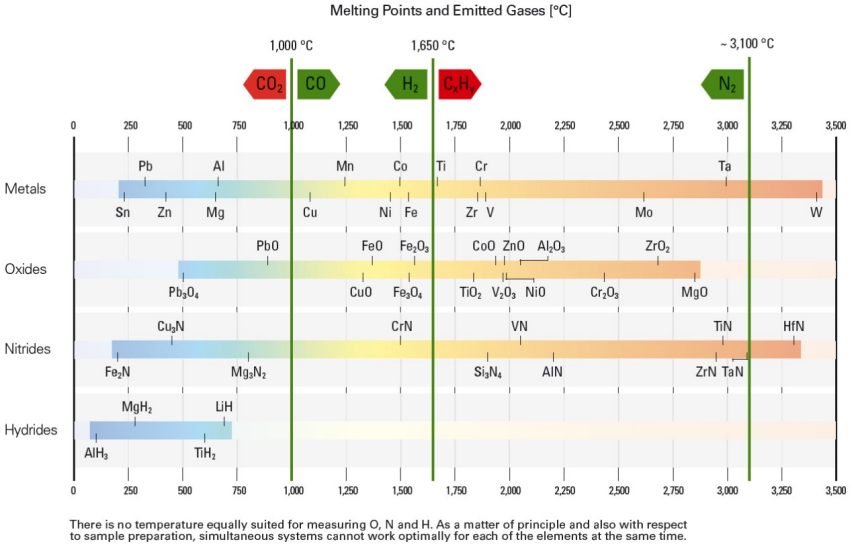
Temperature matters: Melting points of common metals and their oxides, nitrides and hydrides
With the G8 GALILEO analyzers, Bruker is the only company to offer fully integrated ONH solutions combining the benefits of multiple dedicated systems without any analytical compromise or technical limitations. The G8 GALILEO applies the Smart Molecule Sequence™ for direct measurement of all emitted gases and real 1:1 information – without chemical transformations, mathematical corrections or unpublished algorithms. FusionControl, the ongoing contact free temperature measurement of the sample ensures the right analysis temperature, avoiding formation of interfering products and increasing stability and uptime.
Options for automatic sample and crucible handling, electrode cleaning and automatic gas dose calibration are available. When equipped with the unique IR-furnace of the G4 PHOENIX, performs reliable diffusible, residual and total hydrogen measurements and complies to ISO 360 and AWS A4.3 standards for welding.
Key Benefits
- Advanced water cooled electrode furnace with FusionControl, water cooled sample port, high capacity dust trap, followed by efficient in-line particle filtering
- Smart Molecule Sequence™ : Direct and unadulterated measurements of all emitted gases by state-of-the-art detectors with reference channels
- Automatic furnace cleaning, crucible and sample handling available
- Unique external IR-furnace for diffusible hydrogen determination available
- Automatic and reliable gas calibration with 10 different volumes available
- Thermal Desorption Mass Spectroscopy (TDMS) and argon inclusion analysis available by MS coupling
G8 GALILEO – ONH Analysis @ its best
Why do I need Inert Gas Fusion Analysis?
The three non-metals Oxygen (O), Nitrogen (N) and Hydrogen (H) determine the quality, service life and mechanical properties of all metallic materials. Unlike metallic alloy components, the amount of O, N and H sometimes changes considerably along the entire process chain, from the production of raw materials to the completion of the finished product. Similar applies to argon inclusions, introduced at trace level during metal powder production by atomization that will remain in the final product.
Acquiring kinetic information about diffusible hydrogen and its damaging mechanisms are further examples with actual backgrounds like development of new generations of high strengths steels, materials suitable for hydrogen storage or biomedical implants.
G8 GALILEO Applications
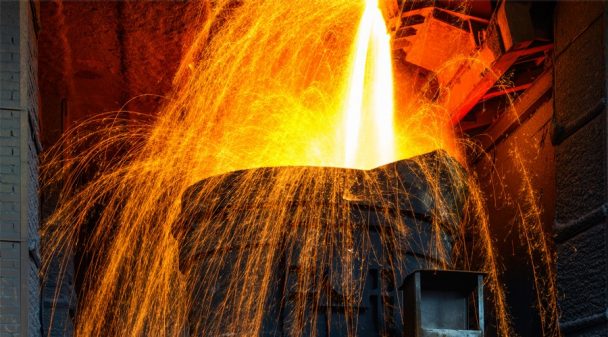
Iron, Steel, Cobalt, Nickel, Ferroalloys
Determining the amount of oxygen and nitrogen is critical during the steel making process, the final alloy adjustment by addition of ferroalloys but also for the production of nickel- and cobalt-base alloys. The G6 LEONARDO combines the ease-of-use and robustness to deliver fast and accurate oxygen and nitrogen results for the Quality- and Process-Control in these production processes.
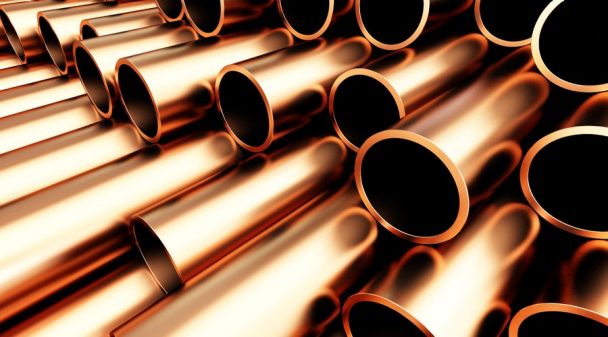
Copper Production
The most important quality factor when grading copper is the level of residual impurities, primarily the oxygen level. High oxygen levels increase the tendency for hydrogen embrittlement and intergranular failure. The Smart Molecule SequenceTM, ensures the G6 LEONARDO analyses oxygen with high reliability and low cost of ownership, while precise simultaneous oxygen and hydrogen analysis is available in dual element configurations with FusionControl.
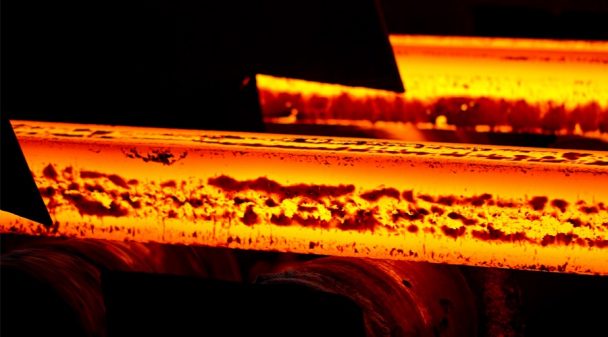
Titanium, Zirconium and other Refractory Metals
Titanium combined with elements like aluminum, vanadium, molybdenum produces low-density, high-strengths alloys with excellent corrosion-resistance. These high performance alloys used in space, aviation, military, nuclear, biomedical and other demanding applications are affected by their oxygen and nitrogen content, but the most critical specification is the hydrogen content leading to hydride precipitation and subsequent cracking. The G6 LEONARDO is prepared to address the needs of these demanding industries.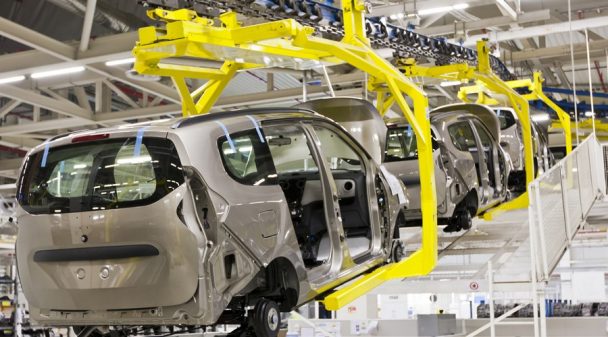
Metal Processing
From stainless steel, aluminum, copper, nickel, titanium to zirconium and further special metal compositions, the G6 LEONARDO delivers vital knowledge about the chemical material composition to every demanding metal processing task in aviation, space, automotive, biomedical, electronic and similar industries.
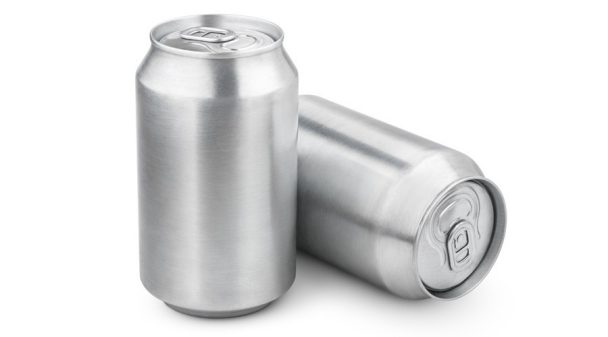
Aluminum and Magnesium
Oxygen and hydrogen play a dominant role during the production and processing of these reactive light metals. Oxygen forms insoluble, refractory inclusions whereas hydrogen, dissolved in the liquid melt, is trapped during solidification, creating hydrogen filled voids and blisters. With its unique FusionControl and SampleCareTM, the G6 LEONARDO is an ideal quality control tool for the aluminum producing industry.
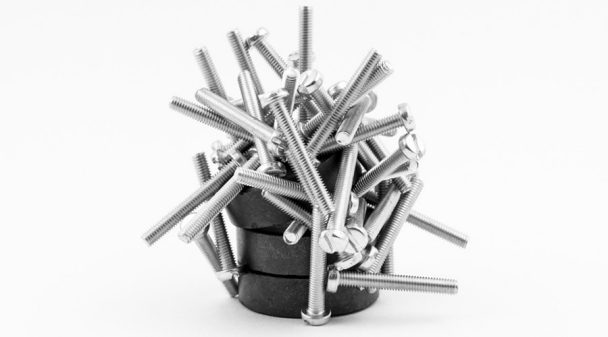
Magnetic Materials
The evolution of high strengths permanent magnets is related to the application of rare earth metals. Sintered Nd-Fe-B magnets show a high tendency to absorb hydrogen, leading to fatal hydrogen embrittlement. Actually, hydrogen is a vital agent in the manufacturing process but is also during recycling of the rare earth metal, while oxygen reduces the magnetic efficiency. The G6 LEONARDO is an economic and easy-to-use tool for process control on both elements during all production stages.
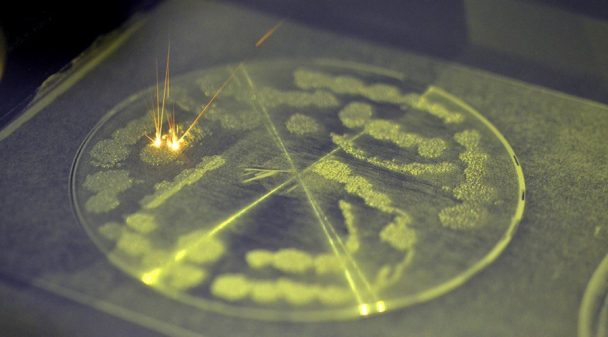
Powder Metallurgy and Additive Manufacturing
Metal powders used in additive manufacturing and other powder metallurgical processes are high purity materials with strictly defined particle properties. Their large specific surface makes them susceptible to “aging” by oxidation/moisture along the production chain with oxygen and hydrogen content dominating the yield rate and product quality. The ready-to-use G6 LEONARDO addresses the needs of such emerging industrial applications.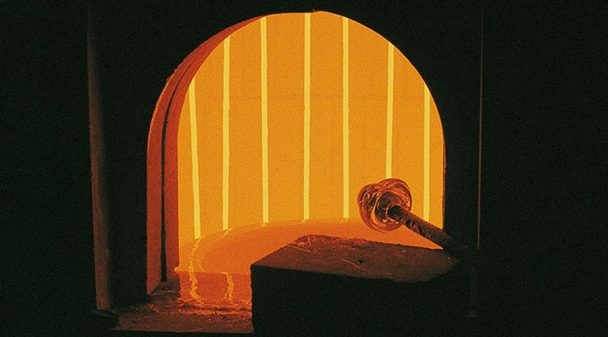
Glass & Ceramics
From industry refractory materials to high performance ceramics in electronics or in metal cutting, refractory oxides, nitrides and carbides have a wide usage. The unique properties of glass and ceramics are influenced in fundamental ways by the level of oxygen, nitrogen and hydrogen present in the process or in the final product. With SampleCareTM, FusionControl and its robustness, the G6 LEONARDO is an excellent tool for the fast analysis of raw materials, intermediates and final products.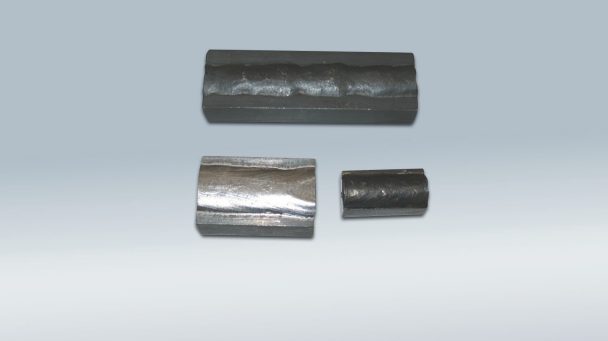
Welding and allied Processes
Bruker’s unique G8 GALILEO IR is supported by ISO 3690 and AWS A4.3 and enables a rapid assessment of diffusible hydrogen levels introduced during welding. Because of its speed, it enables pre-welding experiments on test samples, helping the welding industry to avoid costly failures.
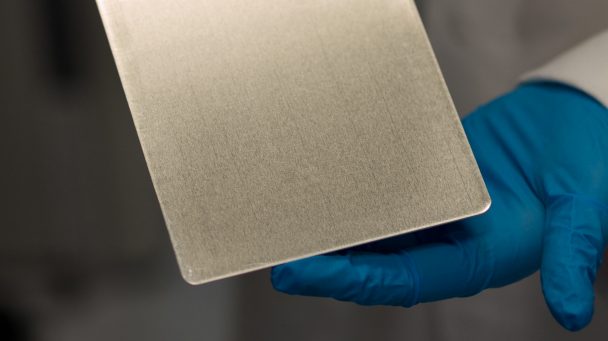
Thermal Desorption Mass Spectrometry
Thermal Desorption Mass Spectroscopy (TDMS) with temperature ramps provides kinetic information like the trapping-energy of hydrogen within a metal structure. Terms like diffusible, weakly or strongly trapped, and chemically bound hydrogen can be directly correlated with the supplied activation energy. Bruker’s unique G8 GALILEO MS is capable to analyze hydrogen or isotopes like deuterium at concentrations of a few ng/g. This enables precise mechanism investigations needed for the development of new alloy generations or alloys suitable for hydrogen storage.G8 GALILEO Specifications
Specification | Benefit | |
---|---|---|
Detectors | ||
Oxygen | Nondispersive IR absorption of CO, no moving parts, dual-range detectors with reference beam and on-board linearization | Reliable, maintenance-free performance without drift |
Nitrogen and Hydrogen | Thermal conductivity detector with reference channel and adjustable gain amplifier | Reliable, adjustable ranges, drift free |
Argon and Hydrogen | Mass spectrometer 1-100 amu, single quadrupole, optimized EI source and channeltron detector | Unique mass spectrometry performance, sensitivity: a few molecules |
Carrier Gases | He (O, N), Ar (O, N), N2 (H) each 99.995 % purity (99.9990 % for trace analysis) | Flexible carrier gas choice without compromises |
Calibration Gas | Pure gases or certified mixtures (99.999 % for each compound), 10 individual volumes in the gas dose device to cover a huge range | Easy, precise gas calibration without standards, directly tracable to fundamental parameters (pressure, temperature, volume) |
Sample Dimensions | Electrode Furnace: 8 x 8 mm cross section (pieces, chips, pins, granules), sample ports available for special applications | |
Cooling Water | Electrode Furnace: 4 l/min at 3 bar supply pressure IR Furnace: 1 l/min at 3 bar supply pressure, 15 – 20 °C inlet temperature, 100 – 240 V / 50 – 60 Hz | Fits on every usual tap water line, tap water-saving design with solenoid valve, chiller also possible |
Power Supply | ||
G8 GALILEO | 400 – 480 VAC (± 10 %), 50 – 60 Hz, 32 A, 7 kVA, 1 Phase plus N or 2 Phase, grounding wire | |
Mass Spectrometer (MS) | 230 VAC, 50 – 60 Hz, 250 VA | Flexible, worldwide power and current configurations |
External Infrared Furnace | 230 VAC, 50 – 60 Hz, 1,500 VA | Flexible, worldwide power and current configurations |
Dimensions and Weight | ||
G8 GALILEO | 80 x 60 x 83 cm (W x D x H), ~130 kg*) | |
Mass Spectrometer | 63 x 64 x 48 cm (W x D x H), ~60 kg | |
External Infrared Furnace | 48 x 66 x 30 cm (W x D x H), ~15 kg | |
*) Depending on configuration |